“There’s something happening here,
What it is ain’t exactly clear”….Stephen Stills
A few weeks ago I published Robotics at a tipping point. The piece focused on how 3PLs like DHL, GEODIS and Quiet Logistics are deploying mobile collaborative robots in their e-commerce fulfillment operations.
One of the things that struck me is that while the implementations we’re seeing are small, it feels as if the market for mobile collaborative robotics is at a tipping point in materials handling, and it feels as if the adoption rate, poised to become in the next three to five years just another tool in the tool kit. In the words of Stephen Stills, there’s something happening here.
Last week, as I was getting ready for Modex, I had a few conversations to learn what’s happening in the piece picking space. I think there are two takeaways: Mobile robots might be an easier sell, but market forces, like the challenges finding enough reliable labor in a tight labor market, are creating conditions that are ripe for automated piece picking; and two, in the right application, piece picking robots are up to the task now. Or, as Crystal Parrott, the newly appointed vice president of Dematic’s Robotics Center of Excellence, put it: “We’re at the very beginning in piece picking.” The caveat: The right application.
The challenge to piece picking, says Parrott, who began her career in robotics at GM in the 1980’s, has been the ability for the robot to “see what a person can see when the robot doesn’t know what’s coming.” For that reason, piece picking robots have primarily been used in manufacturing or distribution applications like case palletizing that involved low SKU counts or low volume products that didn’t have a lot of variation. “In e-commerce fulfillment, you’re dealing with random totes and thousands of SKUs,” she says. What’s changed in the last few years is the low cost of computing, powerful but lower priced sensors, Microsoft opening up the Windows API – it’s core set of application programming interfaces - and “a lot of new open source codes that has enabled new libraries to classify and utilize data.”
Parrott believes the early wins in this space are going to come “from modifications to goods-to-person solutions that become goods-to-robot solutions” and that the long-term winners are going to be “the early adopters who take a slow approach to implementation.”
So, what is the state of piece picking robots? I spoke to three startups with projects that have gone live with their customers.
Goods-to-person picking: Last July, the Wall Street Journal identified the Hudson Bay Company as one of the retailers testing piece picking robots in its order fulfillment processes. The company is already using a goods-to-person engine from OPEX to deliver goods to work stations where people do the picking. The next step, says Leif Jentoft, co-founder of RightHand Robotics, is to use piece picking robots to pick items from donor totes and place them in order totes. “We have customers deploying our system now, and the word is spreading through the industry,” Jentoft says. “People look at the trends, like the growth in e-commerce, and see where labor is going. If they don’t invest now, they’re going to be between a rock and a hard place.” Today’s robots, he says, can deliver on 3 R’s – the range of items, the rate at which the robot can pick and the reliability at which the customer gets the orders.
Jentoft identifies three important developments in mobile piece picking robots. One is flexibility: RightHand, for instance, mounts its robots on a mobile pallet. If the robot completes all of its work in one area, it can easily be moved to another. A second is the ability to integrate the required components into a turnkey solution. “If you’re only delivering part of the solution, like the gripper, it’s hard to identify who is responsible for fixing a problem,” he says. Finally, as with mobile robots, we’re seeing the emergence of “robot as a service” contracts, where the cost of the robot is turned into an operating rather than capital expense. “That aligns the incentives between the customer and the technology provider,” Jentoft says.
The automated putwall: Call it a lack of imagination, but I’d never thought about automating a putwall until I spoke to Vargo about a project they did with Kindred, a robotics startup with offices in San Francisco and Toronto. In it, a robot works side-by-side with associates to assemble orders. While neither Vargo nor Kindred were at liberty to identify the end user, Fortune has reported that the Gap is using Kindred’s putwall technology, and included a video of the solution at work in its story.
“We believe this is the first commercial robotic sortation cell powered by artificial intelligence,” says Greg Williams, Kindred’s vice president of production management and a veteran of Boeing, NASA and Apple. “It sorts batches into individual orders and does so at speeds that are faster than human operators.”
Why a putwall? Williams says that putwalls are areas that are very manual and labor intensive, and, that the Kindred solution is flexible and scalable. “It’s very easy to remove an existing putwall and drop in one of our cells. You can pilot it quickly to prove the solution and determine if there is an ROI.”
Williams says that Kindred uses advanced artificial intelligence to teach the robot how to distinguish between products that may look similar but need to be grasped differently, like a yoga map and an unrolled belt, and to use humans in the loop. “We include a robot control center with a team of robot pilots that can be called in if the robot is presented with an item it can’t pick,” Williams says. The pilot can take control of the robot to complete the pick, and, with AI and machine learning, the robot learns for the next time it sees that same item.
Williams understands that these are emerging technologies. “We recommend taking a small and slow approach and using pilots to prove the technology works,” he says.
Mobile piece picking robots: Last summer, I had a chance to spend several hours with Gary Ritzmann, the project manager at Rochester Drug Cooperative, watching a mobile piece-picking robot from IAM Robotics autonomously – and flawlessly – pick items from a shelf to a tote in one of RDC’s pick zones. What was notable at the time was that, well, it wasn’t just a science project. The robot was working at the same speed as associates picking orders in the adjoining pick zones. Like the Kindred solution, RDC had the equivalent of a robot pilot, an operator who was available in the event of a mis-pick and to induct totes onto a takeaway conveyor. But, as the robot operator told me at the time, most nights are pretty boring – the robot was reliable. Since my visit, the robot has picked almost 50,000 items and its area of responsibility was doubled to two zones.
What is the sweet spot for a fully autonomous piece picking robot? “Right now, we’re targeting applications with low quantities per line and 200 to 300 picks per hour – we’re good for random access but not for super high throughput,” says Tom Galluzzo, IAM’s founder. “We see opportunities in grocery, health and beauty, pharma, small electronics and apparel because of the items that are picked.”
The pushback to a fully-autonomous robot has not been the ROI. “The ROI isn’t why people are first interested innovation,” Galluzzo says. “With the compound growth rate of e-comm and the labor issue, a fully-autonomous robot goes right to the heart of the labor issue.” Rather, the barrier is that a fully autonomous solution, even one that can work in an existing infrastructure without much in the way of modification, requires a real commitment to the technology. That’s one reason why RDC took a slow and methodical approach to rolling out its first robot. Once in place, however, “mobile piece picking robots will allow you to rethink what you warehouse looks like,” says Galluzzo.
About the Author

Follow Robotics 24/7 on Linkedin
About the Author

Follow Robotics 24/7 on Linkedin
About the Author

Follow Robotics 24/7 on Linkedin
Article topics
Email Sign Up
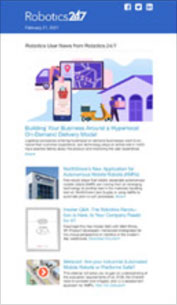