Labor management systems (LMS) have been around for years, making the market a fairly mature and proven one by supply chain software standards.
Used primarily as a way to manage and track the labor activities for distribution operations, LMS typically incorporates real-time interaction with warehouse management systems (WMS). Most often used within the four walls of a warehouse, these systems report on labor activity, and then compare that activity against historical data and established labor standards.
However, despite LMS’ knack for enhancing worker productivity and shaving labor costs, adoption rates for the software have been less than impressive over the last few years. “Historically, LMS was the purview of large facilities with 200 or more workers, with the grocery segment being a particularly large user of these systems,” says Dwight Klappich, research vice president for Gartner, Inc. “And as this history shows, LMS implementation costs have just been easier to justify with larger labor forces.”
But that sentiment could change, says Klappich, as more software vendors offer LMS as part of their supply chain software suites—and as companies across the board strive for improved labor management practices. “Demand for labor management is up, and at the same time the solutions have become more achievable for a wider array of companies,” he says. “As a result, we could see more companies turning to LMS.”
While business activity is picking up nationally, the number of jobs isn’t increasing to meet that growth. Calling this phenomenon a “people-less” recovery, Klappich says companies are using technology like LMS to maintain growth without having to add new employees to the roster.
“LMS is a key productivity tool that addresses labor, and is particularly relevant for logistics professionals that want to be able to do more work with the same number of people, or fewer,” Klappich says. To help companies achieve that goal, LMS creates an environment where worker productivity can be monitored, and adjusted accordingly, to ensure that all employees are performing optimally, and as efficiently as possible.
Over the next few pages, we’ll look more closely at the LMS market and the key issues pushing its adoption inside the four walls as well as in the driver seats of the nation’s private fleets. We’ll also introduce you to a national waste management firm that’s managed to get its arms around driver tracking to create a leaner workforce as a result of its labor management process.
All eyes on labor
In most cases, LMS is used to manage what’s going in within the four walls of a warehouse or distribution center where the highest number of opportunities to track and control labor costs exist.
“There’s so much labor concentrated in the warehouse, and many opportunities to optimize those labor activities,” explains Marc Bessho, consulting manager at supply chain advisory firm Capgemini. “There’s also room for cost reduction and asset utilization—both of which can be tackled by an LMS.”
Klappich concurs, and says vendors like Kronos, Red Prairie, and Manhattan Associates have all honed their LMSs—either standalone, or as part of a larger supply chain software platform—to the point where implementations result in improved human capital management, and better oversight on important factors like time and attendance.
Supply chain organizations that implement LMS frequently experience a “pretty massive upside in return for their investments,” according to Bessho, although convincing logistics managers of that ROI isn’t always easy. “Sometimes it’s a hard sell,” he says. “What many companies don’t realize is that by putting key performance indicators (KPIs) in place to measure worker inactivity, they can gain 30 percent to 40 percent improvements in utilization within the warehouse.”
Couple those gains with the productivity gains that result when a shipper achieves better workforce visibility, and the pay-for-performance associated with engineering labor standards, says Bessho, and the case for LMS becomes even more compelling.
“Using an LMS, companies can track and report on individual performance, and then compare actual versus standard performance,” says Clint Reiser, a research analyst with supply chain technology consultancy ARC Advisory Group. “Using that data, shippers can keep a closer eye on employees and work processes, and use that feedback to make improvements, manage processes more effectively, and create incentive-based programs.”
Brought to you by:
click here to download PDF article
Addressing hang-ups
LMSs come with their own unique set of challenges, most of them cultural in nature. For starters, a “big brother” barrier can come into play when an employee-tracking system is put into place. Warehouses or distribution center sites that are unionized tend to run into the most resistance in this area, according to Klappich, who has seen a few labor forces use their union clout to block the use of LMS in the workplace.
Exactly how the LMS implementation is introduced and rolled out can make or break it, says Klappich, who advises logistics professionals to lead with a strategy that clearly explains how the tools will be used on a day-to-day basis—not as a big brother-type tool, but as a way to solve warehousing labor issues and improve productivity.
“If you just drop this on the workforce, there’s definitely going to be resistance,” says Klappich. “Employees will assume you’re trying to micromanage them, and that you’re going to use the information to fire them.”
Effective LMS implementations also take time, and must be supported by internal standards and processes, says Klappich, who has watched more than one warehouse or distribution site install such a system, only to shelve it a few months later out of frustration. “If you’re going to use an LMS, you have to establish a center of excellence and a support structure for it,” says Klappich. “Without these elements, your LMS will simply become a scorecard for penalizing employees who don’t meet your standards.”
Republic Services: All about empowerment
Republic Services of Phoenix, Ariz., is one company that definitely hasn’t let its LMS gather dust, nor has the system become a point of contention for the waste management firm’s 26,000 employees and 3,800 managers. With locations in 47 states, and more than 50 different divisions under its corporate umbrella, Republic Services uses its Kronos LMS to manage a geographically dispersed labor force with ease.
That decision has paid off for Republic Services, which uses its LMS as a tracking and reporting tool for all man-hours worked to manage its logistics-related labor. The software manages time and attendance processes for employees, and allows the shipper to control labor costs, minimize compliance risk, and improve labor productivity.
Republic Services, which has been using the LMS for several years, migrated its newest acquisition, Allied Waste, to the system in 2008. In doing so, the former added 20,000 new employees to its existing LMS. Previously, Allied was using 63 different eTIME standalone databases to manage its workforce, and the databases were only accessible to their respective users and didn’t provide any type of company-wide visibility.
“When the merger took place, we decided to get everyone on the Kronos system,” recalls Stackhouse, “knowing it would give everyone insights into what was going on across the merged entities.”
Getting there required a conversion, and an upgrade to the latest, web-based version of the LMS. The projects were undertaken concurrently—a move that created a few challenges for the company. For example, Stackhouse says internal IT resources were stretched to the limit during the changeover, which required extensive user training (based on the fact that the company was moving to a web-based system).
“We have a very small team made up of me, and one support person,” Stackhouse explains. “It was a big undertaking, but we really felt it was the right way to go. We knew we could get more gains out of the newer, upgraded system.”
Payroll administrators, dispatchers, and clerks also use the LMS, namely for reporting, Stackhouse adds. The system includes a controlled access function, which allows certain users to edit information and approve data and others to simply print out applicable reports. “With each user role, there is a different security level,” Stackhouse explains.
Rudy Leon, Republic’s HR systems manager, says the LMS has proven itself especially useful when it comes to tracking driver hours and ensuring that employees don’t exceed FMCSA hours of service rules. “We have a lot of safety-related managers who use the system for DOT reporting,” says Leon, “to make sure they don’t exceed the maximum number of hours while driving.”
With 3,800 users currently on its LMS, Republic plans to enhance the system even further this year by implementing a module that will allow the company to test and certify driver time. “While we’ve already seen a lot of benefits from being able to monitor our employees,” says Stackhouse, “now we’re looking to leverage our LMS with additional add-ons.”
Leon sees the LMS as a vital tool in today’s competitive business environment, where companies are continually forced to do more with less. “Through technology,” says Leon, “we can empower our managers to get the data they need to make the best decisions, instead of having to rely on others for that information. That’s invaluable.”
Brought to you by:
click here to download PDF article
About the Author

Follow Robotics 24/7 on Linkedin
Article topics
Email Sign Up
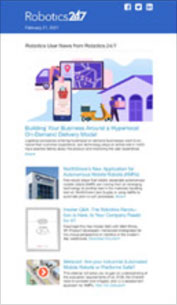