Returns processing is a necessary, tedious and time consuming operation. Hence why it's it a prime candidate for robotic systems.
In 2023, $743 billion in retail merchandise was returned - about 14.5% of sales - according to a National Retail Federation (NRF) and Appriss Retail report. The NRF also reported a full-year retail sales increase of 3.6% from 2022 to 2023.
These hefty dollar amounts showcase just how necessary reverse-logistics operations remain as part of an organization's customer service process.
Bedford, MA-based Berkshire Grey develops robotic sortation systems for retail and e-commerce distributors. In its “2022 State of Retail & eCommerce Fulfillment Report” the company found 72% of executives believed they would lose customers if they didn’t offer free returns, and 80% who saw increased returns in 2020 needed to increase headcount to accommodate.
The survey of chief supply chain officers also found 51% of executives believed implementing automation will increase employee satisfaction, and 43% believed it will lead to a decrease in employee turnover.
Chris Geyer, vice president and fellow at Berkshire Grey, recently spoke with Robotics 24/7 about automated sortation of returned merchandise and other reverse logistics operations. Geyer was previously a research scientist at Carnegie Mellon University and iRobot.
Automation for loose and unpackaged item sortation
Can the same type of equipment be used for both returning and goods-to-person processes?
Geyer: The automation systems that we use to sort goods can be used in multiple workflows in a warehouse.
Could returning and goods-to-person items all pass through one stream instead of two separate streams?
Geyer: It depends in part because of the nature of the goods and the equipment that you're using. For different companies and for different industries, there are different ways in which the returned goods are presented and how they intend to be handled. The ability to handle those SKUs depends on the systems.
One of our customers is in apparel, so the returns that they see are typically unpackaged goods. You open up the mailer in which the item comes, and then you’ve got to figure out what to do with it. This particular retailer had many jeans, so typical automation systems that do both sortation and picking couldn't handle the unbagged jeans, whereas our robotic picking systems could. That was because of the nature of presentation of the goods in the returns through a reverse logistics process.
In the case of those jeans, we can both fulfill them and we can do the reverse logistics. The way that the goods are presented when they're returned can affect where you can handle them in an automated way.
Does non-uniform condition of packages, or even different types and sizes mixed together, add complexity to reverse logistics sorting?
Geyer: Complexity is there in the fulfillment or distribution process, but is worsened by differing conditions of the product. There's perhaps a consumer makeup, or something about the company that impacts that condition. It depends on the company, it depends on the automation systems.
How are Berkshire Grey's sortation systems configured to handle different types of items?
Geyer: Our singulation systems were from the beginning designed to handle a wide variety of goods. At the very beginning - when we developed the technology - went to general merchandisers like Target and Walmart, filled up our shopping cart, and determined the kind of material handling gripping system that will lead to the highest eligibility or coverage of SKUs. As a result of that, we can generally handle the widest variety of conditions in the reverse logistics context.
On the sortation side, we've also designed our sortation systems to have a very high eligibility in general, even outside of reverse logistics. Our automated Robotic Shuttle Putwall (RSPW) was designed to be able to handle shoe boxes. That system can handle those shoe boxes irregardless of whether that's for fulfillment, a distribution operation, or a reverse-logistics operation.
Returning apparel and e-commerce products to market quickly
Are there particular industries or areas where Berkshire Grey's product deployments have been most successful?
Geyer: In the apparel space we've had a lot of success, especially in fast fashion. Our customers want to get the product out to the stores as quickly as possible. We also do general merchandise for store replenishment and e-commerce, so a great variety of goods. That's in part because we are able to handle a great variety of items. Our sweet spot is items that aren't in cases, and eaches that are in the up-to-five-pound range.
Do you know what items your customers see returned most often?
Geyer: In general what we see in those kinds of operations - perhaps more generally in apparel - is that consumers will purchase multiple sizes of the same item, not knowing which one will fit best, and then return the one or two that don't fit. That's the most common if there's any one common thing.
What can Robotic Process Sortation and Identification (RPSi) do to help expedite reverse logistics?
Geyer: Our RPSi system does three things. It does the singulation: pick an item out of a cluttered bin or off a conveyor belt with multiple items on it. Then it has to know where to sort it to, and so in order to do that it's got to scan it. It's able to scan the product automatically by presenting it to a barcode scanner. And then based on the output of the barcode scanner, it determines which cubby or bin to sort the product to.
Our systems do their scanning in a couple of different ways. The way that it works in most RPSi’s is it releases the product that it's picked over a scan tunnel. As the product descends, it's scanning for the barcode from multiple different directions. That's particularly good for poly bags and apparel that would tend to crumple or fold. As the product descends, it can reveal the barcode by opening partially up. We also do scanning by holding the product and presenting it to barcode scanners.
Automating sortation allows employees to handle return fraud
In what ways does Berkshire Grey's robots help cut back on the cost and time of recycling, repackaging, and transporting items through reverse-logistics processes?
Geyer: In the fast apparel industry, you want those items back on the shelves as fast as possible so that they're still current, so that they're not marked down. We work to get those on the shelf as fast as possible by automating the process. You don't need as many people to do the sortation or singulation to get the items back on the shelves, either in the stores or in the warehouses.
Labor of course is a tremendous problem for many of the folks in the warehouses and logistics industry, so we're reducing that labor. There are many steps in a reverse logistics process that have to do with reducing fraud. We let the people who are good at that do that, but we help with the manual handling processes in the reverse logistics workflow.
Would you agree that a lot of the robotic innovation that we're seeing lately is not necessarily to replace jobs, but to ensure human employees’ skills are being capitalized on?
Geyer: Absolutely. In so many warehouses, what we're doing is helping to increase job satisfaction - in many cases by making the processes and the work that people have to do more interesting or easier for them. We've heard instances where people have stayed on longer than they otherwise would have because of the systems that we've installed.
Berkshire Grey launches its 4th generation of systems
What's new with Berkshire Grey's fourth fourth generation of products compared to the previous generation?
Geyer: The fourth generation has a greater number of destinations: up to 100 store locations, so this system is often used in store replenishment. It is faster than the prior generation.
Those are the two biggest desires: faster and more destinations, which are really important to our customers. The more destinations and open orders, the more efficient their upstream processes can be.
What does the future look like for sortation systems going into 2024?
Geyer: More BG systems out there! We're really excited about our fourth generation system. It's got that speed and higher destination count, as well as aspects that increase usability for operators. I think a big thing is to help many more customers impact their upstream processes.
We see the sortation systems essentially allowing customers to do more with existing AS/RS systems that they have, or making AS/RS systems more efficient, which allows brownfield sites to do more with what they have.
At greenfield sites - at new installations - we can do more with the existing storage system or with storage systems that are planned. We can reduce the number of cranes in an AS/RS or the number of robots in an AS/RS by using the sortation system, which allows many, many more open orders than if you just had a goods-to-person station.
Want to learn more about reverse logistics? This article was featured in the February 2024 Robotics 24/7 Special Focus Issue titled “Robots enable more efficient reverse logistics.”
About the Author

Follow Robotics 24/7 on Linkedin
Article topics
Email Sign Up
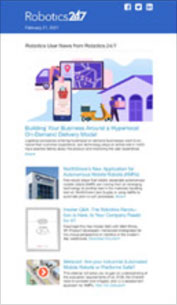
