As increasing e-commerce activity continues to be the “new normal when it comes to emerging supply chain strategies and planning, one thing that comes with that premise, which cannot be overlooked, is the need for more United States-based warehouse and distribution center workers to keep up with growing demand.
That is the main takeaway in research published today by Los Angeles-based industrial real estate firm CBRE.
Entitled “The U.S. Supply Chain Quandary: Finding Enough Workers for an Expanding I&L Sector,” the report’s working thesis indicates that the current e-commerce environment is forecasted to create demand for an additional 452,000 warehouse and distribution workers over 2018 and 2019.
CBRE explained that the 452,000 tally stems from the application of a ratio of one employee per 1,000 square-feet of e-commerce distribution space, which easily surpasses the sector’s job growth of 183,000 new positions per year, going back to 2013 and serves as a barometer of increasing e-commerce sales activity.
Matt Walaszek, Senior Research Analyst at CBRE specializing in Industrial & Logistics and the report’s primary author, said in an interview that with a current shortage of workers, there has still been growth over the years, but looking forward there remains a significant need for more workers.
“We see that already with the truck driver shortage, so there are two solutions,” he said, “ one is to draw workers in from other industries. Data indicates that transportation and warehousing workers are winning on that front, with migration to those areas from other industries, because opportunities for growth are pretty good. Other industries, like retail, are evolving, and we are losing jobs in other sectors.”
The second solution, according to Walaszek, is automation and how it comes into play.
“It is going to be something industrial occupiers need to look at,” he said. “The upfront costs are quite expensive at the moment, and as technology develops, it will make its implementation easier. Certain data shows that the U.S. along with Canada and Mexico are lagging behind some of the other regions in regards to industrial robot shipments, with around 48,000 in 2017 compared to more than 230,000 in Asia-Pacific. This difference is mainly due to Japan having a different attitude towards robots and the other piece is the cost of it and the demand perhaps is not quite there for it. I think that is going to change.”
Walaszek said the overarching trends of e-commerce are driving the need for more workers, coupled with the structural changes going on with regard to the retail sector and the growth of the industrial and logistics sector.
“Then, of course, we also have a shrinking skilled workforce,” he noted. “In the coming decades, there are going to be a lot of people moving into retirement. In regards to transportation and warehousing, that is certainly no exception, with nearly 20% of the supply chain workforce at or near retirement age.”
This does not portend a “doom and gloom” scenario, with Walaszek saying he is hopeful technology will aid in future development, and also being able to attract younger workers, too, while it is occurring at the slower rate than anticipated.
CBRE’s research found that the U.S. markets that provide advantageous combinations of availability, quality, and cost of labor for warehouses and distribution are Memphis, Louisville, California’s Inland Empire, Indianapolis, Atlanta, Nashville, and Dallas-Fort Worth, as well as other markets.
When gauging the key elements for developers and occupiers in making site selection decisions, Walaszek said it is important to weigh the costs versus quality of labor.
“Some of the top markets have seen massive population growth and clearly have high quality labor, however, costs are a lot higher than in the southern markets,” he said. “Some occupiers need to be there, and it is likely there will be a migration to some of these cheaper markets that have a plethora of cheaper labor for lower wages, but, at the same time, high quality workers and workforce availability.”
About the Author

Follow Robotics 24/7 on Linkedin
About the Author

Follow Robotics 24/7 on Linkedin
Article topics
Email Sign Up
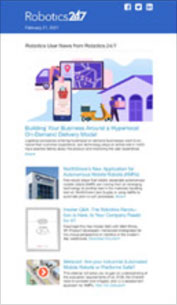