The Odom Corporation
Location: Anchorage, Alaska
Square Footage: 235,000 square feet; 1 of 20 distribution centers of varying size
Products Handled: Beverages including soft drinks, beer, wine and spirits
SKUs: 10,500 active SKUs; more than 30,000 SKUs in Odom’s database
Throughput: 20,000 orders per day, but varies based on seasonality
People/Shifts: 2 shifts per day; 5 days per week
Read the related feature article on Odom Corporation's Alaskan distribution center.
The Odom Corporation’s fleet of 64 lift trucks, with seven more on order, are used in putaway and replenishment, picking and shipping.
Receiving
Receiving happens during the day shift. Given its location, product for distribution arrives by container at the port in Anchorage, Alaska. When containers arrive at the inbound receiving area (1), pallets are unloaded by lift truck and scanned into the warehouse management system (WMS). They are now available in the system.
Putaway
Putaway is system directed. When a lift truck operator scans a pallet, the WMS identifies the storage location. If the item is out of stock in the pick area, it is scanned into a location on the pick line (2). Otherwise, kegs are stored in a cooler area (3), while pallets are stored in selective rack (4) or in the reserve storage area (5) where radio-controlled shuttles choose a location in the 17-deep pallet drive-through rack system.
Picking
Odom delivers full cases, mixed cases and the occasional full pallet. Each has its own process.
Full pallets
Pallets for a full pallet order are scanned and retrieved from the reserve storage or selective rack areas and delivered to the staging area in shipping (6).
Full cases
Full cases are picked from pallets stored at the ground level on the pick line and scanned to a pallet on a pallet jack. There are also ground level pick paths in the reserve storage area.
Mixed cases
Picking of wine and spirits takes place in a three-level pick module known as the bottle room (7). An order begins on the bottom level of the pick module when a case is inducted onto the conveyor system. The case travels through the levels until the case is picked complete and is then conveyed to a staging and merge area (8) where orders are aggregated and retrieved by a lift truck operator.
Packing
Once all of the cases for a pallet have been picked, the pallet is inducted onto an infeed conveyor that feeds an automated stretch wrapper (9).
Shipping
Once pallets are wrapped for shipment, they are staged for loading and shipping.
System suppliers
- Lift trucks, forklift fleet management system, labor management system, pick-to-light and radio-controlled pallet shuttle: Raymond
- WMS: eoStar
- Bar code scanning, mobile computing and voice recognition technology: Honeywell Safety and Productivity Solutions
- Automated stretchwrapper: Wulftec International
- Direct-store-delivery and routing software: Omnitracs (Solera and Roadnet Anywhere)
About the Author

Follow Robotics 24/7 on Linkedin
Article topics
Email Sign Up
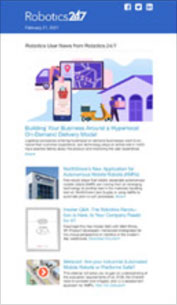
