Robotiq Inc. today announced its PE20 palletizing system, which it claimed is “the most powerful palletizer” in its product lineup.
“With a payload capacity of 18 kg (40 lb.) and stacking heights of up to 2,150 mm (84 in.), this turnkey solution is designed to help businesses effectively scale future operations and achieve a quick return on their investment,” wrote Maude Desjardins, senior manager for product marketing at Robotiq, in a blog post.
PE20 has small footprint
Levis, Quebec-based Robotiq noted that the PE20 is the third automated palletizing system it has released for the packaging industry. Like its predecessors, the PE10 and AX10, the PE20 has a compact design for easy integration and operation.
The PE20's frameless base helps minimize its volume, giving it one of the smallest footprints in the collaborative robotics industry and saving companies from expensive production floor reorganization, claimed the company. In addition, easy access to controllers and cables ensures hassle-free maintenance and troubleshooting, Robotiq said.
The newly designed frame includes fork slots to allow users to move the palletizer before anchoring it for production. The base edges of the PE20 are angled for smoother robot movements, which can be particularly helpful when dealing with pallet patterns featuring overhanging boxes, the company added.
Robotiq noted that the PE20 is designed with photoelectric pallet sensors instead of mechanical sensors, to more easily handle overhang patterns.
Robotiq works to optimize gripper, cobot arm, software
The PE20 is equipped with Robotiq's PowerPick20 vacuum gripper for performance and versatility. The gripper has a high payload to weight ratio, allowing to optimize the net UR20 lift capacity to 18 kg, it said.
“PowerPick20 is the only standard gripper on the market that is designed specifically for palletizing applications using Universal Robots' next generation arm, the UR20,” said Desjardins.
PowerPick20 includes a dual-channel external controller. According to Robotiq, enhanced control over the vacuum flow allows for optimizing multiple case picks as well as slipsheet management.
The gripper kit also includes multiple suction cups along with small and large brackets to accommodate different case sizes. An allen key is all that is needed to set up the gripper, eliminating the complexity and programming required with custom grippers, the company said.
Robotiq asserted that its user-friendly software features a visual interface and built-in modules that guide users through steps, eliminating the need for programming.
Standardization the key to successful deployments
Robotiq said its engineers have elimnated complexities to save customers time and effort. By pre-connecting hardware and pre-programming parts of the software, the company said it also minimizes the risk of malfunction during installation.
Standardization and pre-configuration mean that the user doesn't have to worry about defining geometry, pallet positioning, and signal inputs in order to accurately manage the cell status. Robotiq said its integrated offering reduces the need for custom programming and external expertise.
It added that the Robotiq Palletizing Solution is the result of work done in-house to handle and optimize robot trajectories based on numerous pallet patterns, infeed options, palletized material types, and cycle times. Robotiq said this makes its palletizing system the most cost-effective one on the market.
Article topics
Email Sign Up
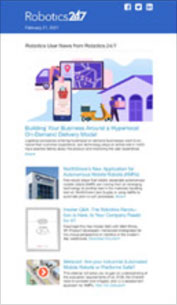
