If your distribution center has grown in both SKUs and order volume or your typical order has shifted from retail to more ecommerce sales resulting in larger requests for smaller orders; it’s possible your picking productivity isn’t where it should be.
You might also be struggling to find the labor to push orders out the door quickly and meet your service level agreements.
These are just some of challenges that companies, both large and small, around the globe are facing as they adapt to market changes and shift fulfillment operations to cater to the latest ecommerce demands.
At this point, you might be considering changes to your order fulfillment process and have heard of different types of picking automation. But, where do you start? Would automation work for your operations?
I’ve worked closely with both local and national customers as they explore moving their operations from standard, manual picking to automated processes. There are four key steps that help to evaluate and identify the right automation for distribution centers.
1. Data Gathering
Start with data. Gather up order data from past months and years. The goal is to get good insight into future picking requirements. We aim to predict the future requirements up to five years in the future.
Data lists you’ll want to pull include:
- SKU master list with dimensional data to see what kind of volume is required.
- Order profiles with items picked, quantities, and lines on the order.
Data not only gives us insight to your current and future throughput and fulfillment needs but also helps us to find creative solutions to challenges that extend to the distribution facility itself.
As businesses grow, it is inevitable that the building you once thought to be plenty big for expansion, can no longer accommodate needed operations. Physically, you might be running out of room for product storage and performing manual handling operations.
Instead of spending a great deal on a building expansion or a new building all together, automation solutions such as pick modules, ASRS or other goods to person technology can be utilized to make better use of the available building space.
Many of these technologies leverage vertical space to allow a higher percentage of the building volume to be used. This increases the overall value per square foot of the building, giving you more room to accommodate business success.
2. Current Picking
Making changes to your operations gives you the opportunity to evaluate how things are done currently and how you might want or need that to change. Start by evaluating how you are picking right now and what rates you are picking at currently in lines per person hour. How many people does it take to pick your current volume?
Most automation solutions help to increase the product flow rate through a building. Equipment like conveyor and robotics allow products and orders to flow though at higher speeds and decrease the amount of touches. This means that the maximum amount of orders that can be fulfilled in a day now has room for growth.
If demand for the product is currently not the limiting factor for the business, then more orders can be processed using automation. This of course leads to an increase in revenue. The same can be said for diversity of products offered. If customers are demanding new items, automation can help to not only process this new demand in time, but also provide the space necessary to store the goods.
3. Working through the Information
Provide your information to a qualified expert to take a look at your operations and evaluate your options. Automation technology continues to change and so do the combinations of solutions. Any material handling project or consultation for your business will include a series of questions and information gathering to best get to know not only which automation options will fit, but what your specific business needs.
The questions will cover:
- Data – order demand, inbound activity, inventory snapshots, item master lists, staffing and layout.
- Growth – financial and operations growth.
- Business characteristics – unique details of your business.
- Decision criteria – budget, potential related costs, targeted ROI period, current staffing and productivity, for example.
4. Confirming a Solution that Fits
As you work through the process of evaluating distribution center automation solutions, make sure you understand the data analysis and that forecasts are reasonable. Make sure the solution would make sense in your environment and challenge it if it does not. Challenging helps to ensure you are working towards the right solution and that the investment is solid.
Ways to challenge:
- Check seasonal data for outliers you need to consider
- Future-proof with discussions about upcoming business development, expected growth, new product lines, etc.
- Ask the questions that you may assume are already addressed – can help confirm or validate
Decision: Make the Move
Increasing order quality and meeting your service level agreements goes a long way to satisfying customers, reducing costs and driving future growth success. Recognizing your operations are in need a change is step one. Once you’ve done your research and have explored various solutions, it’s time to make the decision that will help your business stay competitive. Don’t be left in the dust.
Related White Papers
How to Ease Labor Challenges with Advanced Automation
Automation can help a retailer handle everything required with their unique e-commerce fulfillment challenges. Download Now!
Microfulfillment Strategies – Top Priorities for Retailers
Consumers’ buying patterns have changed the game for retailers - COVID has supercharged the demand for online shopping, same day or even within the hour delivery. Download Now!
Article topics
Email Sign Up
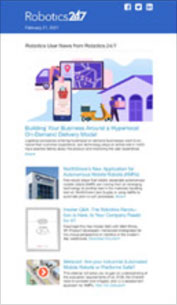
